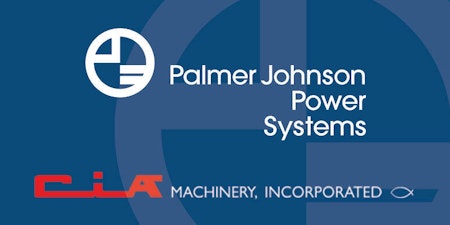
6 Key Steps to 5S Sustainability
5S is a pillar of any Lean Environment. In early 2014, Palmer Johnson committed to a lean transformation journey within our Service Department. In order to prepare for this transformation, we worked closely with Tom Barrett of Lean Partners. Our goal was to create a culture of continuous improvement. Palmer Johnson wanted a consistent best-in-class customer experience from our Service Department. We found at the time that our lead times were not where we wanted them to be. We also found that we were struggling to keep up with our increased customer demand. In order to be best-in-class for our customers we needed our Service Centers to get to a new level of organization that was much higher than what it had been in the past. It is an age old story in lean that waste in your process leads to a messy environment which stifles continuous improvement. What PJ found was no different. The key to a culture of continuous improvement was cleaning up as much waste in our process as possible and getting to a level of 5S sustainability. Once you have reached this level of sustainability it becomes very easy to keep a shop organized, create standard work and focus your continuous improvement on what can improve the customer experience. At Palmer Johnson, we strive to be the best. You will find we are never satisfied and will always be in a process of lean transformation but the focus around continuous improvement in our shops has led to all kinds of positive change. We have seen tremendous improvements in quality, safety, lead-times, communication and overall employee morale. We have also found that 5S creates space from the re-activeness of the day to day and puts our Service Centers in a proactive creative space where they can innovate around how to get better. This inward innovation we believe is what leads to outward innovation and an overall best-in-class service for our customers. Here are the 5 key concepts we have learned that helped us reach our 5S goals:Set a 5S goal: What are you trying to accomplish and why? For Palmer Johnson we set a goal to get all Service Centers to a 5S level of Sustainability and to reach Showcase at our headquarter location in Madison, WI. Setting this goal required us to map out what the goal was and to put a plan in place to get there. We wanted a measurable goal that could be communicated and Lean Partners suggested we use a 25-point auditing process. An Audit score of 20 or above would be considered sustainable and the last 5 points would lead to a perfect Showcase environment. Weekly 5S Auditing: The weekly 5S audit is key to sustainability and it must be done by service personnel. Tom Barrett from Lean Partners helped us conduct several training's with our Service Personnel to ensure they understood how to conduct a 5S audit. 5S Auditing is really a process of waste identification. Doing this process weekly forces your people to look at the work environment through the lens of an auditor and to begin to see waste in the process. You want this process to be quick and done consistently so you can spot trends and progress. When performed regularly you begin resolving messes early on and noticing problem areas that need improvement. You also spot safety issues early on and prevent accidents from ever happening. The audit process can be focused by zone or can be done on a larger scale. Either way you choose to audit you begin to spot areas that need continuous improvement and you can resolve them before they impact your customer. Daily Stand-up Meetings: The daily stand-up meeting is a challenging feat to ensure it is brief and value-added. It is absolutely essential though in 5S that you at least have one brief 5S meeting a week. It is best conducted at a whiteboard to review your audit and list out areas for improvement and begin assigning ownership. The meeting is not the place to problem solve on what you think the solution is, it is solely intended to discuss the audit and where the team needs to focus the continuous improvement efforts. By having regular discussions, the team begins to take ownership of fixing these problem areas. These meetings should encourage team involvement and participation and they should also be held to under 15 minutes. Consistency is key so set a time conduct them weekly, ensure the audit is complete and you will undoubtedly see progress.
Kaizen Newspaper: The Kaizen Newspaper is a tool for ensuring that problem areas get listed out and that improvements are being made weekly. This should also be discussed in the 5S Meeting. What are the improvement areas we need to focus on for next week and what improvements were made the previous week? This sheet should be posted on the whiteboard and team members should be encouraged to add ideas to the list as they come up with them. This promotes the culture of continuous improvement and it helps generate ideas for improvement. Deep Dive into Problem areas: Doing the weekly 5S Auditing, the Daily Stand-up meetings and the Kaizen Newspaper consistently will lead to lots of great ideas. This will encourage teams to deep dive into problem areas and this is where you will really begin to move the needle. These types of efforts are proactive and they must be prioritized they can be time consuming and are often needed most when you are behind. Problem areas collections of waste and they impose all kinds of side effects on your culture and environment; ultimately these areas bleed out on your customer experience. You want to be sure that when you deep dive into an area you go far enough that it is visually sustainable. Stick with it: 5S is a process and it is going to take time, the key is consistency and measuring it as you go. At Palmer Johnson we set our goal of reaching sustainability at all locations in 2014 and reaching Showcase at our Madison, WI location in 2014 (Video tour of Palmer Johnson HQ.) It took more than a year to accomplish and a commitment from our entire organization. This process will never be complete continuous improvement has become part of our DNA. We are never satisfied this has lead us to two straight years of excellence in safety with zero accidents, and a 99.5% quality rating it has also lead to over a 20 day average lead time reduction. DOWNLOAD: 5S Templates
If you would like to learn more about Lean concepts or 5S in general here are a few good resources:
Gemba Academy: Great library of online training videos on the topic of lean.
The Gold Mine: A Novel of Lean Turnaround by Freddy Balle
Lean Partners: Consider conducting a Kaizen event with Tom Barrett and his team.
Keep Reading
PJ News
Palmer Johnson Power Systems Acquires CIA-Machinery Inventory to Expand Drivetrain Support Capabilities
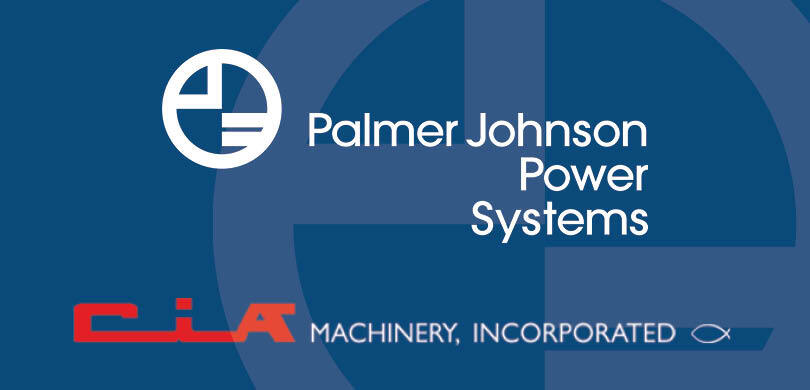