AGCO Reman Program
We recently went to AGCO's Batavia, IL parts distribution headquarters to participate in AGCO's monthly dealer live streams. This live stream focused on Reman, below I have highlighted the main points that were covered in this meeting.
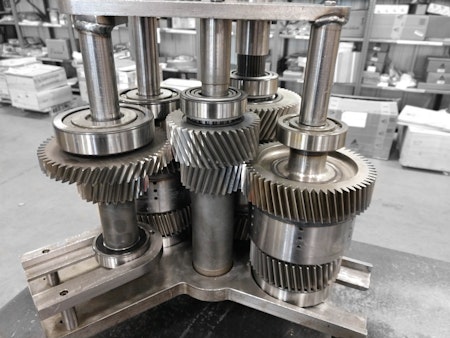
Why Reman?
- Less downtime
- Extends the life of older equipment
- Built to OEM specifications
- Performs like a new component
- Peace of mind with a warranty
AGCO Reman Process
When a core comes to Palmer Johnson from the AGCO core return center, our initial step is to do a full inspection of the unit. Next comes the complete tear down and further inspection. There are some parts, wear parts, that we will always replace, such as gaskets, seals, O-rings, friction clutch plates, bearings and charge pumps. During the tear down, our technicians will also note what additional parts need to be replaced. The unit is torn completely down to the bare housings, cleaned, inspected, wear items discarded, updates performed, key wear points are measured for reuse or scheduled in our machine shop for repair. During this process our Service Technicians document everything in the service report. Parts and then sourced and ordered or sent to the machine shop for repair.
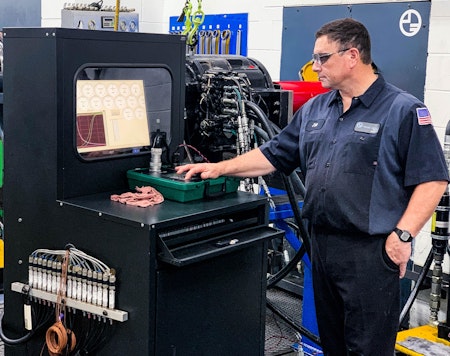
Our Machine Shops gives PJ the ability to not only update parts, but to save damaged housings and shafts. This helps us keep our costs low and gives us the ability to continue offering remans when new parts are no longer available.
After we have all the new/updated parts, our techs begin the rebuilding process using the required special tooling. This tooling allows us to do the job safely, correctly and without damaging any parts. Our use of the correct special tools ensures that the critical adjustments are made correctly during the buildup process without damaging any parts. During the rebuilding process, our technicians will also make any and all updates to the unit. Once the unit is rebuilt, it is tested to factory spec’s. This testing provides piece of mind that the unit will work trouble free when it is back in the field. To learn more about our testing process,click here.
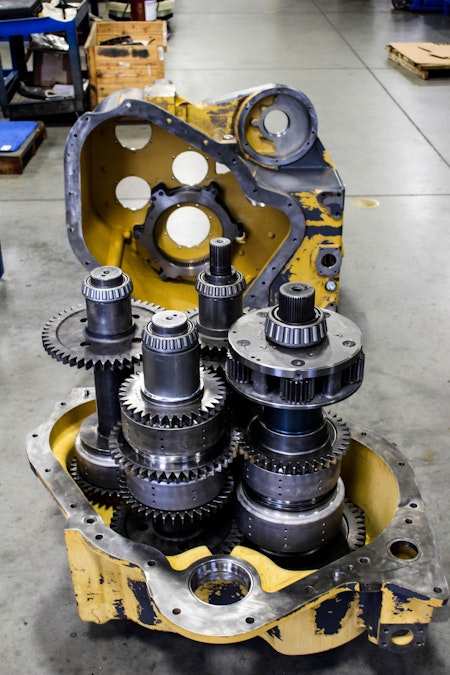
Transmission Failure in Ag Tractor Example
A common error happens when the owner starts that the transmissions is making an odd sound when in 3rd, 6th or 9th gear, or it won’t pull into those gears, so the owner just doesn’t use those gears. In reality, what is happening is that the failed clutch pack is still turning and as the clutch plates continue to run against each other, they are creating a lot of debris inside the transmission. As they continue to use the machine, they are slinging the debris throughout the transmissions, causing more damage to what would have been good parts had they stopped using the machine as soon as they knew they had a problem. The longer this goes the more likely that contamination will end up getting into the differential, brakes, and hydraulic systems and damaging those as well, thus taking a $14,000 repair and running it up to $35,000 - $60,000 or to scraping the entire tractor due to such a high repair cost.